Understanding Stall and its Effects in Steam Systems
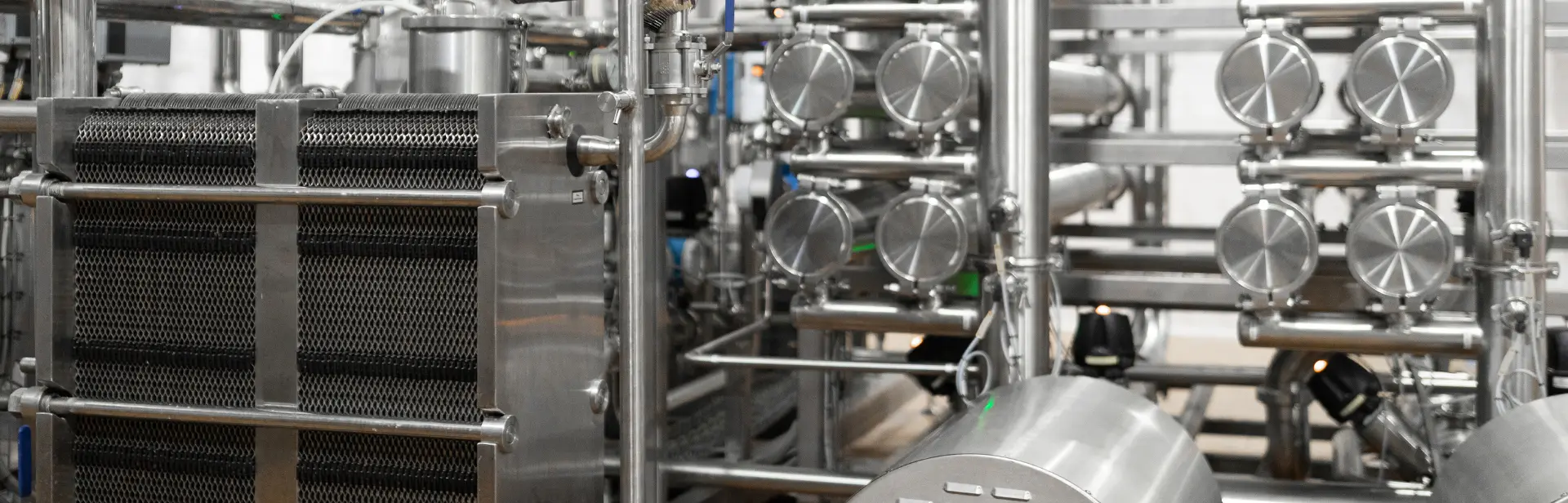
‘Stall’ is the inability to evacuate condensate effectively from the heat exchanging equipment. The expectation that the condensate should be evacuated from the heat exchanger as soon as it is formed is adversely impacted when the pressure in the heat exchanger is equal to, or less than, the total backpressure acting on the outlet of the steam trap installed on the heat exchanger.
Stall occurs when differential pressure across the steam trap becomes negative. During stall condition, the steam operated pump trap uses external motive steam to create a positive pressure for evacuation of condensate. When differential pressure across the trap is positive, it evacuates condensate by functioning as a float trap using the two orifice mechanism that is capable of handling condensate, both at peak loads and very low running loads.
In most heating applications, the process media has to be heated from the initial lower temperature (most often ambient temperature) to its final set temperature. Here, the secondary fluid inlet temperature rises as a result of the falling heat load.
During the start of the process, as shown in Fig No.1 below, when we have maximum heat load, the differential pressure across the steam trap remains positive and it facilitates the condensate removal.
As the control valve reduces the steam pressure to meet a falling heat load, the lack of differential pressure across the steam trap causes condensate to waterlog in the steam space. This is illustrated in Fig No. 02 below.
Problems Caused by Stall
Water logging of condensate in the process equipment
Water logging reduces the effective area available for heat exchange hence the overall heat transfer
coefficient will reduce.
This results in:
- Poor heat transfer
- Increased steam loads
- Fouling/ corroding of heat exchanger
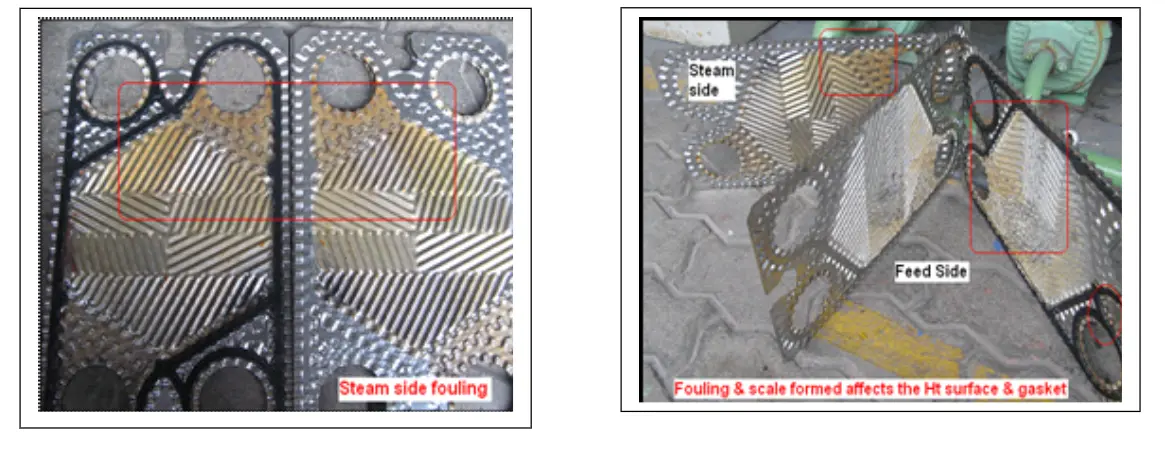
Image: Fouling in the PHE
Gasket Failure
Stall conditions lead to negative pressure inside the heat exchanger, causing waterlogging of condensate that could lead to failure of gaskets. Gasket failure results in unsafe operations and maintenance hassles, besides adversely impacting equipment uptime.
Hunting of Temperature Control Valve
When process temperature is not properly sensed, the temperature control valve operates frequently. This leads to ineffective and unstable temperature control for the process.
Inadequate Product Quality
Lowered heat output and unstable temperatures across the heat exchange surface can impact product quality, and most often plants suffer with lower yield.
The Forbes Marshall Solution
Conventional steam traps cannot remove condensate unless the trap bypass valves are kept open. The opening of trap bypass valves result in higher steam consumption. A properly sized Steam Operated Pump Trap (SOPT) ensures complete condensate removal during stall conditions without opening of bypass valves. This results in enhanced productivity due to consistent pasteurisation temperature and steam savings of 5-7% at equipment level. Condensate load of the process equipment defines the trapping capacity and computation of stall load based on the operating parameters defines the required pumping capacity. Another important factor to consider during the selection of SOPT is the available installation head, which is a site specific parameter. A range of SOPT variants are available to give a reliable solution for stall in varying condensate flow rates, stall loads and installation heads.
Principle of Operation

Working Principle: Steam Operated Pump Trap