Essential Troubleshooting for Float Type Steam Traps
Steam traps are critical components in any steam system, playing a crucial role in maintaining efficiency and preventing issues like water hammer and reduced heat transfer. Among the various types, float type steam traps are widely used, especially in process applications for their ability to discharge condensate continuously and handle heavy startup loads. A ball float trap operates by sensing the difference in density between condensate and steam. A float rises or falls with the condensate level, opening and closing a valve to discharge it.
However, like any mechanical device, they can experience issues. This guide, drawing from expert sources, provides a detailed troubleshooting approach for common float type steam trap problems.
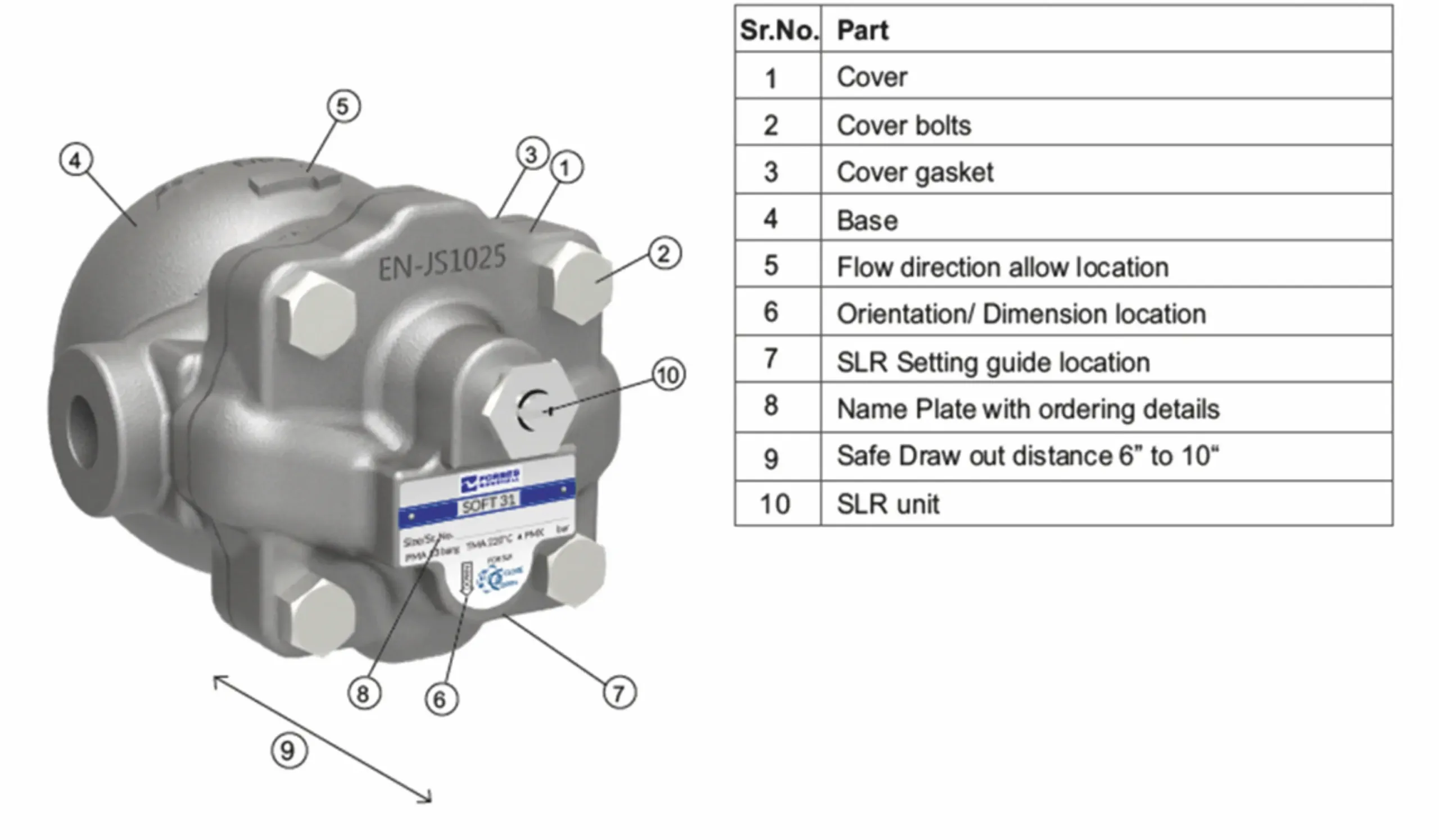
Parts of a Float Type Steam Trap
Common Failure Modes in Float Type Steam Traps and How to Fix Them
1. Float Trap Not Discharging Condensate At All
Symptom 1: No condensate is being discharged, and the trap’s surface temperature is low.
Possible Causes & Recommended Actions:
- Incorrect Installation Direction: The trap might be installed incorrectly.
Action: Check the installation direction arrow on the cover casing and the nameplate arrow on the base casting to ensure correct orientation. - Strainer Blockage: Debris or dirt might be clogging the strainer.
Action: Check for blockage in the strainer and clean it. - Insufficient Differential Pressure: The actual differential pressure across the trap is lower than the design pressure, preventing the float from buoying sufficiently.
Action: Verify the differential pressure. If it’s too low, the float buoyancy might not be adequate to open the valve seat. - Valve and Seat Assembly Issues: The valve or seat assembly might be stuck or damaged.
Action: Check the valve and seat assembly for blockage and clean as needed. - Punctured Ball Float: The float itself may be damaged and no longer able to float.
Action: Check if the ball float is punctured. If so, replace it. This is critical to avoid water hammering in the process. - Stalling: The trap might be experiencing a “stall” condition where the pressure in the heat exchanger prevents condensate discharge.
Action: Make sure the steam trap is not stalling. If stalling is occurring, replace the trap with a steam operated pumping trap, which can overcome adverse pressure conditions.
Symptom 2: No condensate is being discharged, but the trap’s surface temperature is high.
Possible Causes & Recommended Actions:
- Steam Lock Release (SLR) Setting: The trap might be “steam locked” if the steam lock release (SLR) mechanism is not functioning correctly.
Action: Adjust the steam lock release (SLR) setting, typically by first closing it fully and then opening it by 1/4 turn.
2. Float Not Discharging Enough Condensate
Symptom: The trap has a reduced condensate discharge capacity.
Possible Causes & Recommended Actions:
- Undersized Trap: The trap may be too small to handle the peak and running condensate loads.
Action: Check for back pressure and corresponding discharge capacities as per the capacity charts provided by the manufacturer. - Leaking Traps or Connections: Other leaking or non-working traps in the system or issues with back pressure can affect the overall discharge.
Action: Repair or replace any leaking and non-working traps. Also, investigate if a higher back pressure on the working traps connected to the same return line is hindering discharge.
3. Flooding of Condensate
Symptom: Condensate is accumulating and flooding the system.
Possible Causes & Recommended Actions:
- Open or Leaking Bypass Valve: A bypass valve that is open or leaking, especially in a closed loop, can cause back pressure and flooding.
Action: Ensure that the Non-Return Valve (NRV) is installed on the outlet of each trap. Additionally, ensure all bypass valves are closed or not leaking, as an open bypass increases back pressure on the trap. - Blocked Inlet Strainer: Debris can obstruct the inlet strainer.
Action: Check to see if the inlet strainer is partially blocked and clean it. - Blocked Thermostatic Valve Seat Orifice: The thermostatic valve seat orifice might be blocked.
Action: Check for blockage, clean, and lap if necessary. - Blocked Main Valve Seat Orifice: Similar to the thermostatic orifice, the main valve seat orifice can also get blocked.
Action: Check for blockage, clean, and lap.
4. Leaking Steam
Symptom 1: Live steam is observed leaking through the outlet.
Possible Causes & Recommended Actions:
- Incorrect Installation Direction: Similar to discharge issues, improper installation can lead to steam leakage.
Action: Check the installation arrow (item 6 in the diagram) on the nameplate, which should point downwards. - Deposits on Valve/Seat Assembly: Dirt, scale, or other deposits can prevent the valve from sealing properly.
Action: Check the valve and seat assembly for any deposits, clean, and lap. - Damaged Seating Area/Ball: The seating area might be worn or the stainless steel ball on the seating area could be damaged.
Action: Clean and lap the seating area. Lightly stamp an SS ball on the seating area if needed. - SLR Leakage/Setting: Issues with the steam lock release (SLR) can cause steam to pass.
Action: Check for SLR leakage or setting issues. - Air Vent Leakage: The air vent mechanism might be leaking.
Action: Check for air vent leakage.
Symptom 2: Steam is leaking from the joints between the base and cover.
Possible Causes & Recommended Actions:
- Loose Bolts/Damaged Gasket: The cover bolts might be loose, or the gasket between the base and cover could be damaged.
Action: Tighten the cover bolts (item 2 in the diagram) to the recommended torque. If the gasket is damaged, replace the gasket.
Maintaining Peak Performance of Float Type Steam Traps
Regular inspections and periodic maintenance are crucial for float type steam traps. Visual inspections, along with checking for proper condensate discharge, can help identify problems early. By following these troubleshooting steps, you can ensure your float type steam traps operate efficiently, contributing to overall system performance and energy savings.