Steel Industry
Iron Making
The iron making section in a steel plant is the fundamental stage where iron ore is converted into molten iron, which is the primary raw material for steel production.
The raw material primarily consists of iron ore, coke (a carbon source), and limestone (a flux). The blast furnace is at the core of iron making where the raw materials are processed under intense heat.
The chemical reactions within the blast furnace reduce iron oxides in the ore to molten iron. The output is molten iron, also known as “hot metal,” which contains impurities like carbon, silicon, and manganese.
Common problems in iron making include:
- Excess heat is required as nitrogen does not participate in combustion.
- High fuel consumption with low burner zone control.
- Higher operational costs due to unpredictable water leaks from tuyeres.
- Higher coke consumption, leading to increased coal requirements.
- Uncontrolled moisture in the cold blast can cause furnace damage.
- Less heat available for effective iron ore reduction
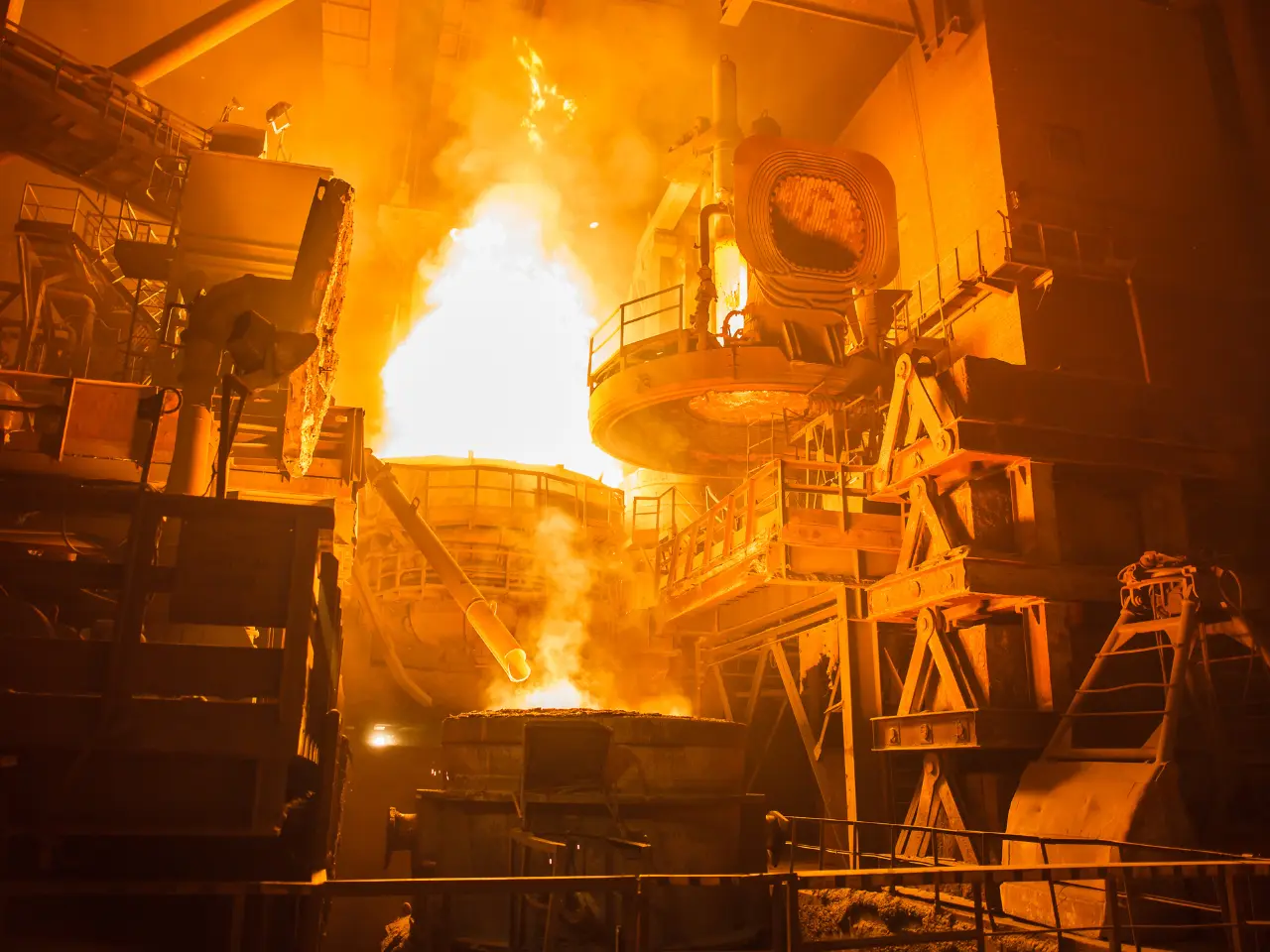
Our Solution:
Forbes Marshall solutions in the iron making section include: