Losing condensate without even realising it? Here’s how smart insights can stop the drain.
Steam systems don’t always lose efficiency because of leaks or equipment failure. Sometimes, it’s small lapses in operating discipline that cause the biggest losses. In many plants, especially those running multi-utility equipment (steam, water), one such oversight leads to condensate getting drained directly into cooling towers or water circuits, reducing the Condensate Recovery Factor (CRF) and increasing the cost of steam generation.
Here’s what typically happens: during a process, equipment may use steam initially, then shift to water depending on the need. While the utility source changes, the outlet needs to be switched as well, from the condensate return line to the water system and vice versa. However when this switch isn’t made at the right time, hot condensate, rich in recoverable energy, gets drained with cooling water. This seemingly small process error can lead to a 1–3% increase in fuel consumption and a noticeable drop in CRF.
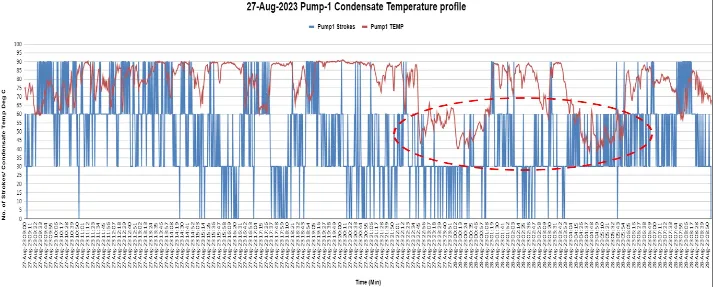
Condensate loss to cooling tower
EverSense for Condensate Recovery Factor, a Forbes Marshall Digital solution, helps you become aware of, and fix, this hidden inefficiency.
By closely tracking patterns, this solution highlights sudden or recurring drops and helps isolate the equipment responsible. Through this live data, our domain knowledge experts guide the user team to identify the root cause. Forbes Marshall suggests corrective action and helps establish SOPs to ensure the process error doesn’t reoccur, locking in efficiency gains for the long term. This kind of operational insight empowers user teams to not just react, but proactively avoid losses.
With Forbes Marshall Digital plants can turn a passive process into a monitored one — one where condensate is accounted for, recovered, and put to use again. In energy systems, small actions drive big savings. And effective monitoring with actionable insights ensures those actions happen, every time.