Enhancing Steam System Efficiency at One of the World’s Largest Breweries
One of the largest beer-producing plants in the world approached Forbes Marshall to identify bottlenecks and develop strategies to meet its energy reduction Key Performance Indicators (KPIs). To enhance the safety and efficiency of its steam system operations, the plant required a comprehensive framework and an actionable plan. Its objective was to develop a system capable of improving and sustaining both energy and process efficiency.
Engineers from Forbes Marshall meticulously assessed the plant’s requirements, conducting an energy audit to establish baseline metrics and identify areas for improvement. They provided detailed engineering support for the implementation of solutions and maintained engagement with the plant over a year to ensure sustained benefits. Their research facilitated the development of a condensate and flash recovery system, improvements in steam quality, and optimisation of waste heat recovery. Additionally, the implementation of a performance management system significantly enhanced the plant’s operations and maintenance practices, proving to be a highly beneficial decision.

What to read next
Products
Associated Services
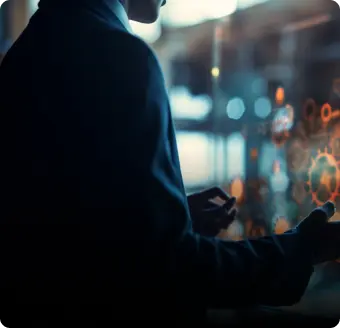
Process Optimization

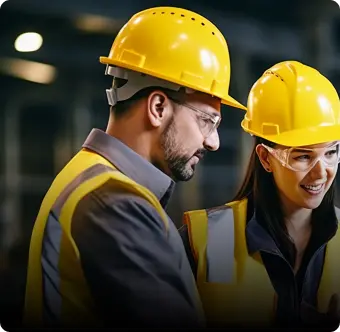
Improving Uptime

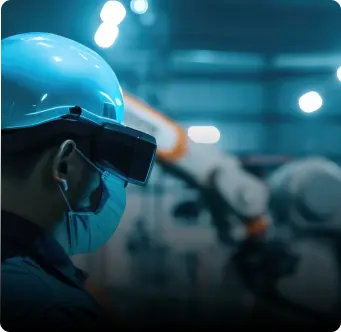
Forbes Marshal Digital
